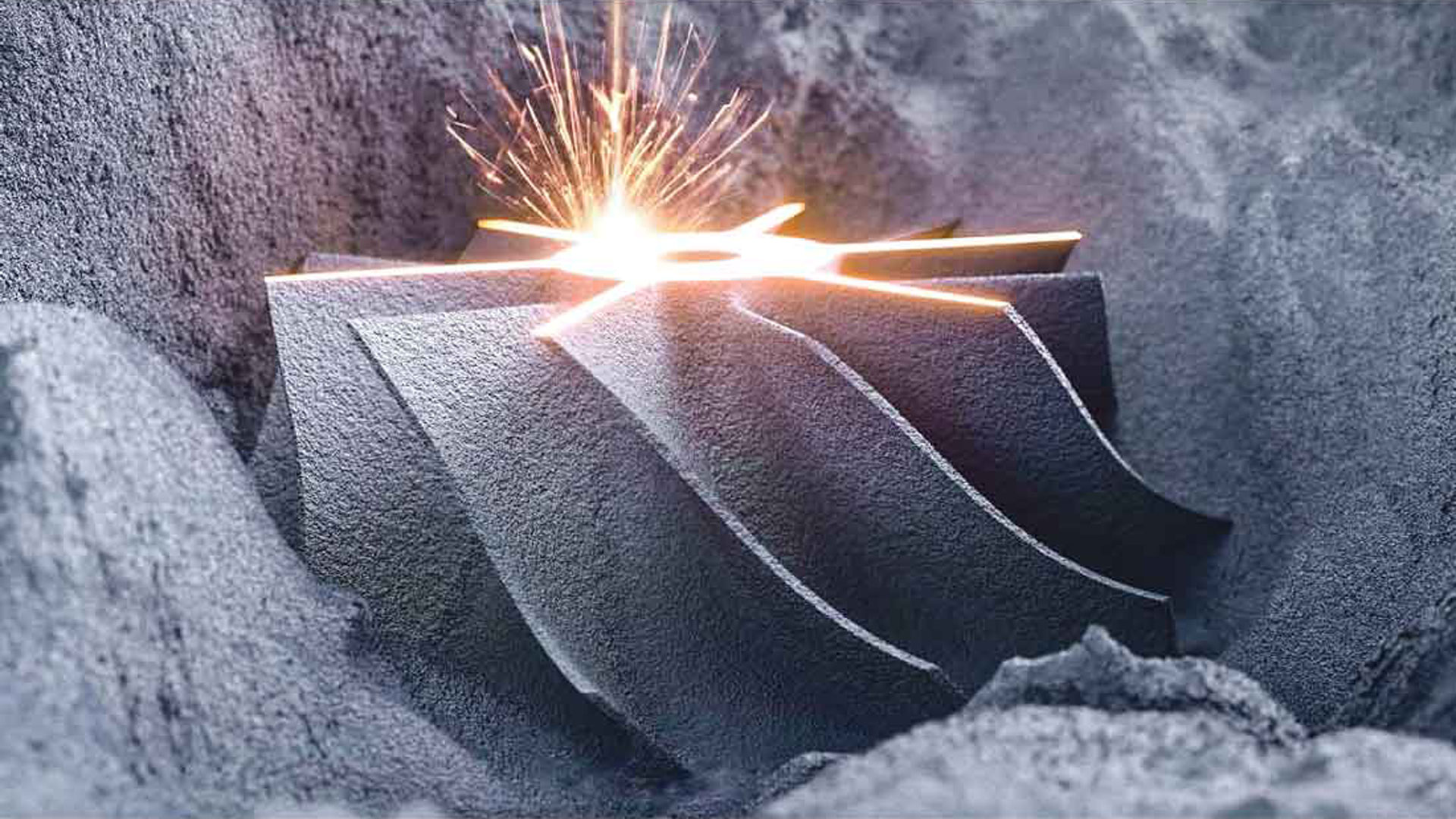
Neutron Radiography
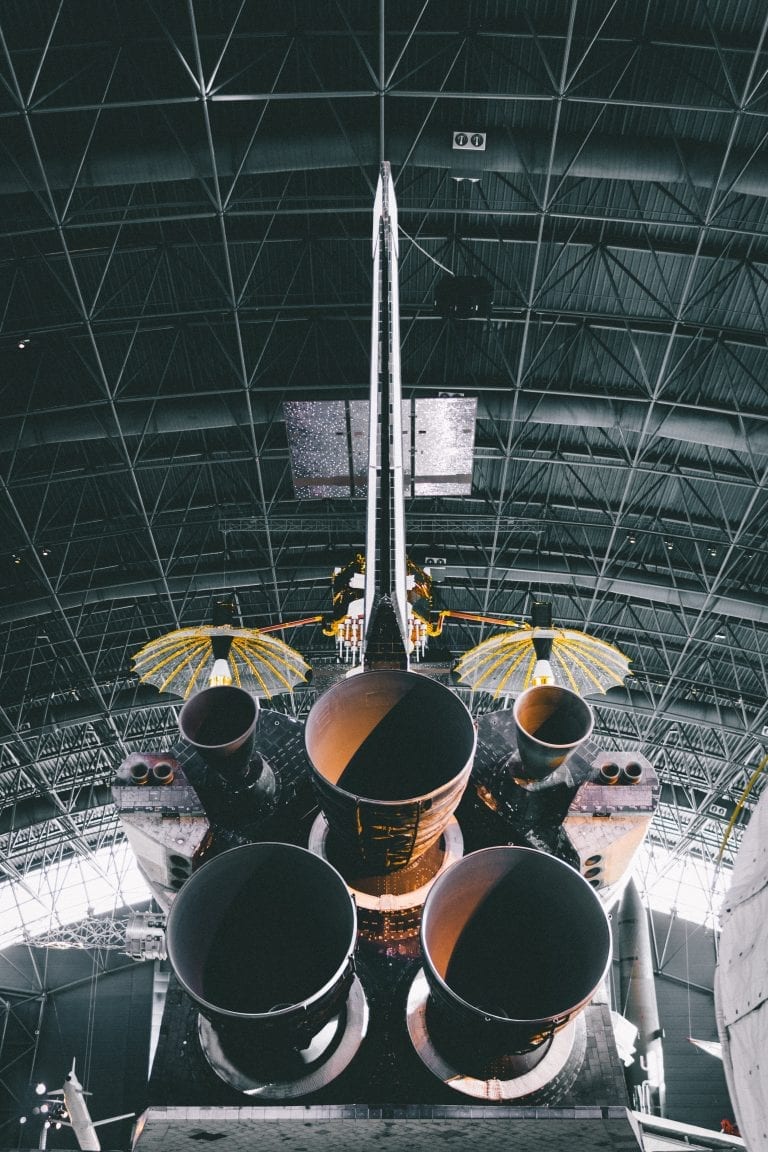
The growing pressure for the aerospace industry to deal with rising fuel costs, be more environmentally sustainable, and deliver higher performance for lower costs spurs innovation. A sizable portion of this innovation today is being driven by two major disruptive technologies: First, new composite materials that make lighter, stronger designs possible; second, additive manufacturing and 3D-printing that makes creating composite components for aircraft and spacecraft easier.
Revolutionizing an industry is hard work, but fortunately, we here at Phoenix have plenty to offer that will make that hard work easier. Read on to learn more about the disruptive potential of composites additive manufacturing and how neutron radiography, or N-ray, can help the innovators in aerospace do their very best.
Composites, Aerospace, and Neutron Imaging
Composites are constructed from a combination of materials that, together, are more than the sum of their parts. A composite material can possess both the durability of one of its constituents and the flexibility of the other, with both materials combining to augment each others’ strengths and prop up each others’ weaknesses.
For example, using a carbon fiber reinforced polymer for the body of a small airplane instead of aluminum alloys results in a plane that is both lighter and stronger, and thus faster and more fuel efficient. Lighter, stronger composites are also a huge boon to spacecraft, freeing up extra weight that can go towards its payload (it takes ten thousand dollars to send a pound of material into space!).
Neutron Imaging: An Indispensable Tool for Composites Manufacturers
When the aerospace industry wants to have its cake and eat it too, composites manufacturers are the chefs responsible for making that cake. Like any great recipe, it takes trial and error to develop composite materials and extensive testing.
The nature of composite materials—as one material encased or embedded within another—means that radiography is a necessary part of testing components made from composites to detect any flaws or unforeseen issues. Radiography and tomography are nondestructive forms of materials testing which penetrate the material with high-energy radiation to “see” inside it.
X-rays are the most common form of radiography, but have some blind spots. Mainly, while they can image a composite made up of a denser material encased by a lighter material, for example, the other way around is a bit trickier. Dense materials stop X-rays dead in their tracks. Neutron imaging, or N-ray, works together with X-rays to help fill in the blanks, since neutron radiation passes through dense materials.
In some circumstances, a single two-dimensional N-ray image can provide as much information regarding a composite’s composition as an entire three-dimensional CT scan.
Are you a composites manufacturer who wants to learn more about how Phoenix can help you?
Get in touch with us to learn more about how neutron radiography can help you create better composites:
How N-Rays Benefit Additive Manufacturing
Additive manufacturing, known more colloquially as 3D printing, is a rapidly-growing service which promises to disrupt many manufacturing industries, including aerospace and healthcare.
Industrial-grade additive manufacturing lays down one thin layer of powder which is melted together by a laser or electron beam and hardened before the next layer is applied, and so on and so forth. The process of converting the powder into a solid mass is called “sintering.”
Hobbyist 3D printing aficionados are more familiar with additive manufacturing that relies on molten PLA or ABS plastic which is deposited in layers to sculpt an object. However, additive manufacturing can utilize all sorts of raw materials, including metals, ceramics, polymers, and even “bio-ink” made from living cells to craft objects.
Additive Manufacturing’s Role in the Aerospace Industry
While traditional manufacturing works best for high-volume production, one of the biggest benefits of additive manufacturing is how quickly and cheaply it can produce low- and medium-volume products, especially complex objects that are difficult to fabricate otherwise.
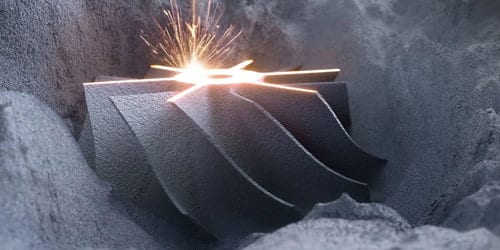
Unlike traditional subtractive manufacturing, which sculpts an object from a larger mass of material, additive manufacturing builds it from the ground up with less wasted raw material.
Aircraft and spacecraft components created through additive manufacturing tend to be lighter, too, and designs made from composites (for example, components with ceramic exteriors and metal interiors) can be easier to construct using 3D printing. Additive manufacturing can construct lightweight, durable parts, such as turbine blades for aircraft engines, heat shields for spacecraft, and tools for astronauts to use in the harsh environment of space.
Over the past few decades, additive manufacturing has evolved from a method of creating nonfunctional scale models for prototyping to a powerful tool both for rapid prototyping and for creating functional products. However, defects in 3D-printed parts can prove difficult to detect.
Due to the relative newness of the industry, researchers are still working hard to better understand how the materials used in additive manufacturing interact and how the likelihood of flaws and defects cropping up can be reduced.
How Better Neutron Imaging Means Better Additive Manufacturing
Like any other manufacturing method, additive manufacturing does not always produce a flawless product. If the powder that makes up each layer of an additively-manufactured object does not sinter together properly into a solid mass, the end result can be structurally unstable. The weaker sections of the object that did not properly solidify cause internal strain, which in turn can bend, warp, or even break it.
Detecting defects matters a lot in the aerospace industry, where a component that fails in mid-flight can lead to a horrendous disaster that puts pilots and passengers in danger. To that end, nondestructive testing is a critical part of aerospace manufacturing, and neutron imaging is a powerful, albeit underutilized testing method.
Using a directed stream of neutron radiation to see through complex materials can catch many flaws and defects that would go completely unnoticed through other means of testing, such as structural weaknesses in 3D-printed components.
Are you a additive manufacturing professional who wants to learn more about what neutron imaging can do for you?
Get in touch with us with any questions you might have about our N-ray services:
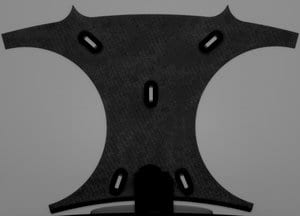
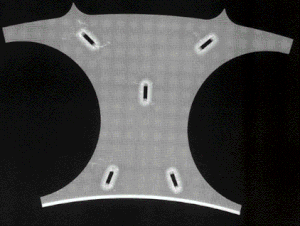
Who Disrupts the Disruptors?
Historically, neutron imaging has relied on research reactors, nuclear reactors owned and maintained by universities, to bombard products with neutrons.
However, the availability of research reactors has never been high to begin with, since there are only a handful of them in the US and their owners only have so many resources to spare toward commercial purposes.
And nuclear reactors—power-generating and research reactors alike—are all under threat of sudden shutdown with no replacements lined up. This is a huge issue for all aerospace manufacturers, some of which only have one source for neutron imaging.
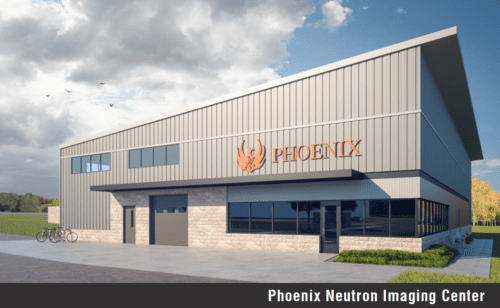
Phoenix, LLC has spent over a decade developing neutron generators which provide neutron flux and fluence without the need for a reactor and has been offering neutron imaging services since 2012.
Our compact neutron generators have already changed the game for many manufacturers in aerospace, defense, and other industries. The upcoming Phoenix Neutron Imaging Center (PNIC) in Madison, Wisconsin will make neutron radiography even more accessible and convenient than ever before.
With the advent of PNIC and the opportunity for future neutron imaging centers to propagate, aerospace manufacturers already accustomed to utilizing N-rays can diversify their options and breathe a sigh of relief, while manufacturers who have currently lacked the opportunity to take advantage of neutron radiography can finally do so.