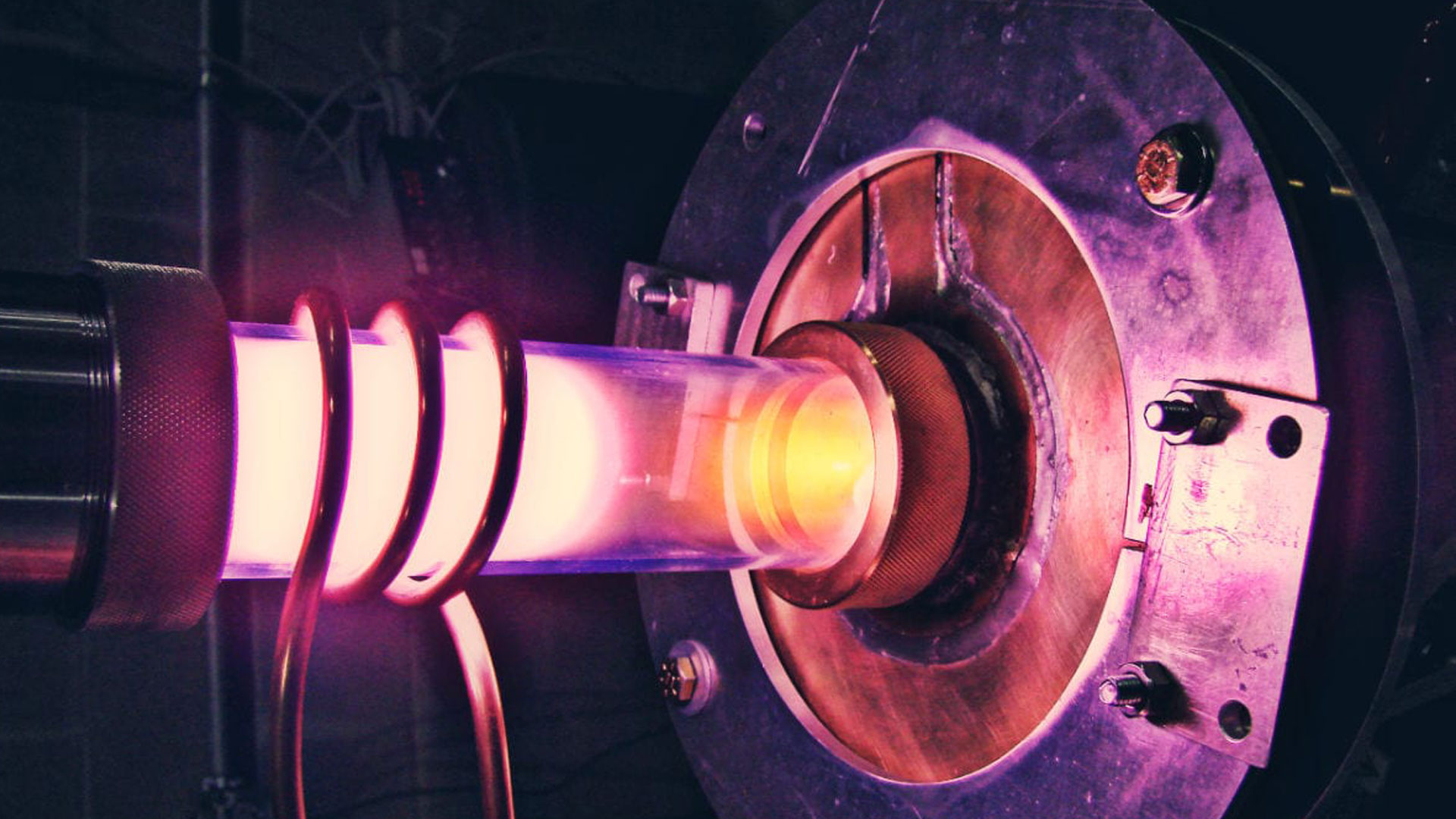
Neutron radiography, or N-ray, is the use of neutron radiation to image materials for nondestructive testing. Put simply, neutron radiation is like X-ray radiation, but neutrons can penetrate dense metal better than X-rays. However, N-ray is underutilized in the auto industry. What possibilities can more accessible, readily-available neutron imaging unlock for automotive manufacturers?
As part of a nondestructive testing professional’s toolkit, neutron radiography is a powerful tool for quality assurance, failure analysis, and research and development. When you need to build a better mousetrap—or in this case, better fuel injectors, batteries for electric cars, etc.—the tools you have at your disposal can make all the difference.
In every manufacturing industry, neutrons are underutilized for nondestructive testing due to accessibility issues. Currently, the primary sources for neutron imaging are nuclear reactors that have been set up for research purposes and can be “rented out” by manufacturers for testing. There are only a handful of them in the entire United States and they are primarily run by universities and graduate students. They are powerful, but difficult to use. Since their primary objective is research, the owners of these reactors have few resources to allocate to commercial applications.
Over the past few years, Phoenix has developed neutron generators powerful enough to provide more than enough neutrons for neutron imaging, providing a convenient and more accessible alternative to reactor-based radiography. With our one-stop neutron and X-ray CT imaging facility, the Phoenix Neutron Imaging Center (PNIC), we aim to drive more usage of N-ray throughout the nondestructive testing community, especially among NDT professionals who work with the auto industry.
Neutron Imaging in the Auto Industry Today and Beyond
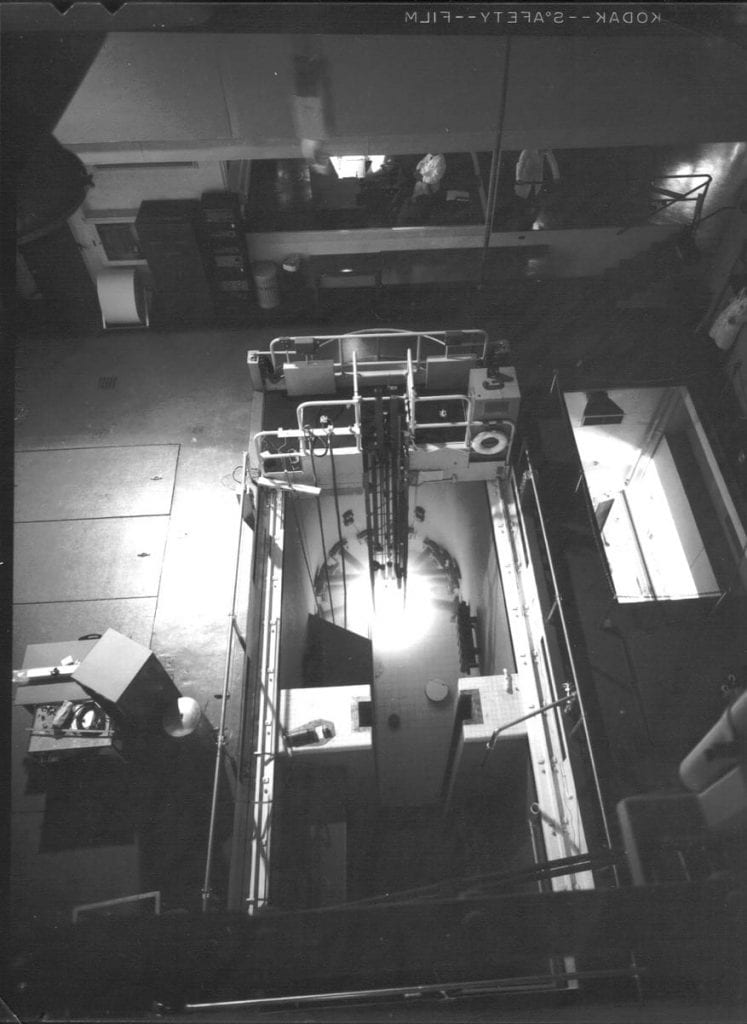
Until it was decommissioned, the University of Michigan’s Ford Nuclear Reactor was an instrumental nondestructive inspection resource for the Big Three Detroit automakers. Among other things, this reactor produced radioisotopes such as bromine-82, which could be used as a tracer to track the movement of oil within internal combustion engines. Due to the costs and difficulties associated with reactor-sourced neutron imaging, N-ray was only used sparingly by the auto industry.
Neutron images pick up on details that two-dimensional X-rays and three-dimensional CT scans might not, which can prove instrumental in detecting flaws in a product’s design or issues arising in the manufacturing process. However, the reliance on the sparse number of research reactors, all of which could be decommissioned at any moment, creates a bottleneck that makes the cost of neutron imaging—the cost in money, time, regulatory burdens, etc.—much higher.
Currently, the high barriers to entry surrounding neutron imaging keeps it from being utilized to its fullest potential for higher-volume tasks, such as quality assurance. But with more accessible facilities, neutron imaging could play a much bigger role in the auto industry than it does now.
With the opening of PNIC (and future facilities based on its design), a viable alternative to reactor-facilitated neutron radiography will be available—one that will be more accessible, with lessened regulatory hoops to jump through, and one that more manufacturers in the automotive industry will be able to take advantage of.
What will it look like when the automotive industry starts using neutron imaging for nondestructive testing? It might look a little like this…
Mitigating the Next Big Recall – A Possible Overlooked Use for Neutron Imaging
When you need to figure out why a component in your vehicles has failed, neutron imaging is quickly becoming more readily available for use in NDT.
But failure analysis is only one way N-ray imaging can be used in the auto industry.
More accessible neutron imaging means quicker turnaround on quality assurance tests for critical components coming off the assembly line, potentially catching disastrous flaws in these products before they end up inside millions of vehicles.
Looking at the biggest auto recalls of 2018, you’ll find culprits such as seatbelt components that could spark fires, steering-wheel bolts that could come loose, faulty airbag control units and brake actuator pumps, and stuck valves in fuel pumps.
Some of the flaws that can lead to recalls like these present themselves right off the bat, while others are the result of unforeseen wear on the components over time. They may be due to an inherent shortcoming of the design itself or a defect introduced in the manufacturing process.
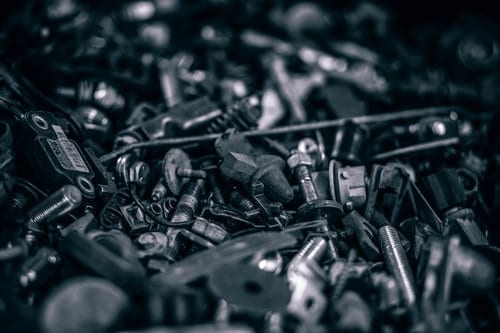
For some of these components, neutron imaging may be the idea method for detecting their flaws before they make it out of the factory, just as neutron imaging is essential for the manufacturers of aircraft turbine blades.
The automotive industry is low-cost and high-margin; many components are cheap to produce and materials testing can cost more than it costs to fabricate them, especially when more methods of testing are added to the quality assurance gauntlet. This is what made neutron imaging previously a tough sell for quality assurance purposes.
Even with Phoenix’s neutron imaging services, using it to catch issues other methods of materials testing might miss still means piling on the costs, and that’s enough to make anyone balk.
But an ounce of prevention is worth a pound of cure. So how much does a recall really cost auto manufacturers?
The Cost of a Recall
The number of vehicles recalled per year numbers in the tens of millions. In 2017, recalls were issued for over 30 million units in total. This was the fewest number of recalled units since 2013; however, only 17.6 new vehicles were actually sold, meaning that 74% more cars and trucks were taken off the road than were put on the road.
There are a few reasons why so many cars and trucks are getting recalled in recent years. Cars are getting more complex, and more components means more points of failure. More regulatory pressure and pressure to act on consumer complaints means more vehicles are being recalled for issues that might not have prompted recalls in the past. And auto manufacturers are sourcing many of the components for their vehicles from the same manufacturer, which means one batch of components with a design flaw or undetected issue can end up in just about every brand of vehicle from Acura to Volkswagon.
Recalling millions of cars is hard work. It’s time-consuming, labor-consuming, and costly. Through a long and involved process involving a lot of committees, manufacturers identify serious-sounding consumer complaints, investigate the component that seems to be at fault, determine how many vehicles sold have that component, decide whether the issue is truly dire enough to warrant a recall, and send out recall notices—by snail mail!—to all affected owners.
That’s the hard part, but what comes next is no better. Actually getting those recalled vehicles off the road can be like pulling teeth, especially when owners are so inundated with recall notices that they stop taking them seriously. Once a vehicle has been recalled, though, it has to be inspected and/or repaired at no cost to the owner (someone has to pay that bill, though…).
In 2016, the total cost of recalls among automakers and suppliers in the US was over $22 billion in claims and warranty accruals.
On top of that come class action lawsuits that might have to be settled with hefty payouts, although that only tends to happen in dire circumstances… for example, Takata’s airbag recall.
Do You Recall the Biggest Recall of All?
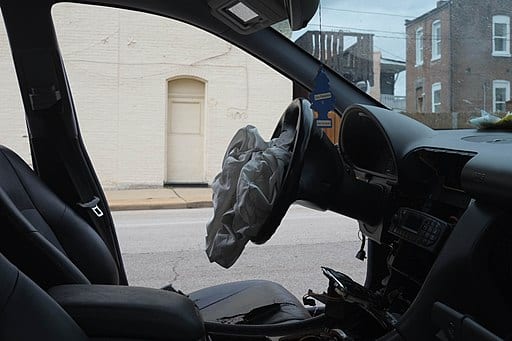
Takata, a Japanese company founded in 1933, was one of the largest auto safety parts manufacturer in the world. After eighty years in business, it became the main supplier of airbags to just about every major player in the automotive industry. Unfortunately, in 2013, defective airbags began to flow out from its factories and into cars and trucks the world over.
From 2013 to 2017, Takata rolled out airbags with a dangerous flaw. The airbags used an ammonium-nitrate mixture to provide a tiny explosive charge and inflate the bags in the event of a crash. However, these chemicals degraded when exposed to heat and humidity over a long period of time, eventually exploding and sending shrapnel flying at the drivers and passengers.
Media outlets jumped on characterizing every vehicle with Takata airbags in it as not only a ticking time bomb, but a literal car bomb—sensational perhaps, but not quite inaccurate. The unexpected breakdown of ammonium nitrate produced a more potent propellant than intended. Eventually, when a crash occurred, the inflators would not fire but rather explode. Seventeen people were killed worldwide by the very devices meant to protect them. Tens of millions of vehicles were recalled over the years.
Unfortunately, Takata’s oversight did not have anything to do with a lack of access to neutron imaging. They knew from the beginning that ammonium nitrate was ill-suited for long-term use in airbag inflators and were well aware of its instability under certain circumstances.
They used it anyway because it was cheaper. But it ended up costing them much, much more than they’d bargained for.
Collateral Damage
At the end of the recall, the consequences to Takata were severe. After all, not only had it spent four years knowingly distributing these defective products, it had also failed to take action when it became aware of the defects and instead kept mum while continuing to sell the airbags to vehicle manufacturers. The sheer volume of class-action lawsuits against it drove the company into bankruptcy and its surviving assets were snatched up by its competitors.
Overlooked, though, were the recall’s effects on everybody else. Vehicle manufacturers whose only sins were buying airbags—airbags that, for all they knew, worked perfectly—were the public faces of the recall, since they were the ones who had to put out recall notices on all affected vehicles.
Most people didn’t know the name “Takata.” But they did know “Ford.” They did know “Toyota.” They did know “Chrysler” and “GM.” And those were the names that were attached to these recalls. These manufacturers didn’t suffer a fate as dire as Takata, and rightly so, but they still felt the same sting they feel whenever a recall is announced—a loss of public trust and potential sales, as well as eating the not-insignificant monetary cost of getting these dangerous vehicles off the road.
Possibilities for Neutron Imaging in Auto Manufacturing
A small object that’s up close looks bigger than a large object that’s farther away; the danger it poses seems direr, even if the larger object is objectively a greater threat. Likewise, it’s hard to conceptualize the cost of a pound of cure when the cost of an ounce of prevention is staring you in the face. Especially when that ounce might seem more like a pound… or ton.
We at Phoenix intend for PNIC and future neutron imaging facilities like it to be the ounce of prevention.
That’s not to say that N-rays can catch everything, of course. Neutron radiography isn’t a cure-all—it just offers a more complete picture of a given component and what might be wrong for it, especially when used in conjunction with other forms of NDT. It is simply the best way to see through objects with dense, metallic outsides and lighter, less-dense insides, making it an ideal materials testing tool for all sorts of gadgets and widgets—especially when it comes to energetic material, such as the tiny explosive device that triggers an airbag to inflate.
Could neutron imaging make it easier for vehicle safety parts manufacturers to catch dangerous flaws in their airbags?
Phoenix has a long history of working with defense and aerospace manufacturers to make sure that energetic devices function properly. And we aren’t just talking about munitions, but also ejection mechanisms and other systems that rely on tiny explosive charges that need to work 100% of the time—not unlike the propellant in an airbag.
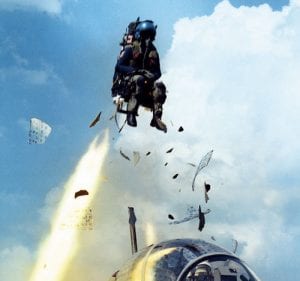
The ejection mechanism in a fighter jet, for example, relies on shaped explosive charges that propel the pilot out of the plane. If those explosives don’t work properly, the pilot could be injured or killed. Fortunately, neutron imaging can diagnose problems with the mechanism before it ends up inside an aircraft.
How Neutron Imaging Can Help Airbag Manufacturers
Samples of energetic material always undergo rigorous long-term testing during R&D to make sure the chemical propellant lasts as long as it’s supposed to without unexpected breakdowns or other issues. Neutron imaging is a critical tool for conducting these tests and assessing the longevity of solid propellants.
An airbag’s inflator is a metal tube filled with tablets of chemical propellant that are ignited in the event of a crash, which converts the propellant into a gas and injects it into the airbag, inflating it. Neutrons can pass through the metal tube but not the propellant tablets; as a result, neutron imaging shows the size and shape of the pellets.
When the solid chemicals in an energetic device break down, their size and shape changes. Cracks and bubbles can form in the material, the material could shrink or expand in size, or the material could even crumble into dust. These all denote a change in the composition of the material which could lead to it either producing too large of an explosion or too small. Using neutron imaging during long-term viability testing, NDT professionals can see all of these warning signs. The shortcomings of a propellant could be discovered and understood in the R&D stage, prompting a redesign of the product with a more stable propellant.
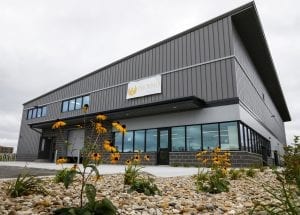
Why Phoenix for Convenient Neutron Imaging?
Phoenix’s compact neutron generators, developed and refined in our labs for over a decade, are a titanic shift from the nuclear reactors typically relied on for neutron imaging. Their neutron output is higher than any other fusion-based neutron source and their compact size and greater accessibility renders them a convenient neutron source. With PNIC and more neutron imaging centers springing up in the future, options previously out of reach for the automotive industry could become well within the realm of possibility.
Only time will tell what effect the expanded use of neutron imaging might have on the automotive industry. We welcome the opportunity to test parts from automakers and suppliers to explore what possibilities N-ray has to make our cars better.