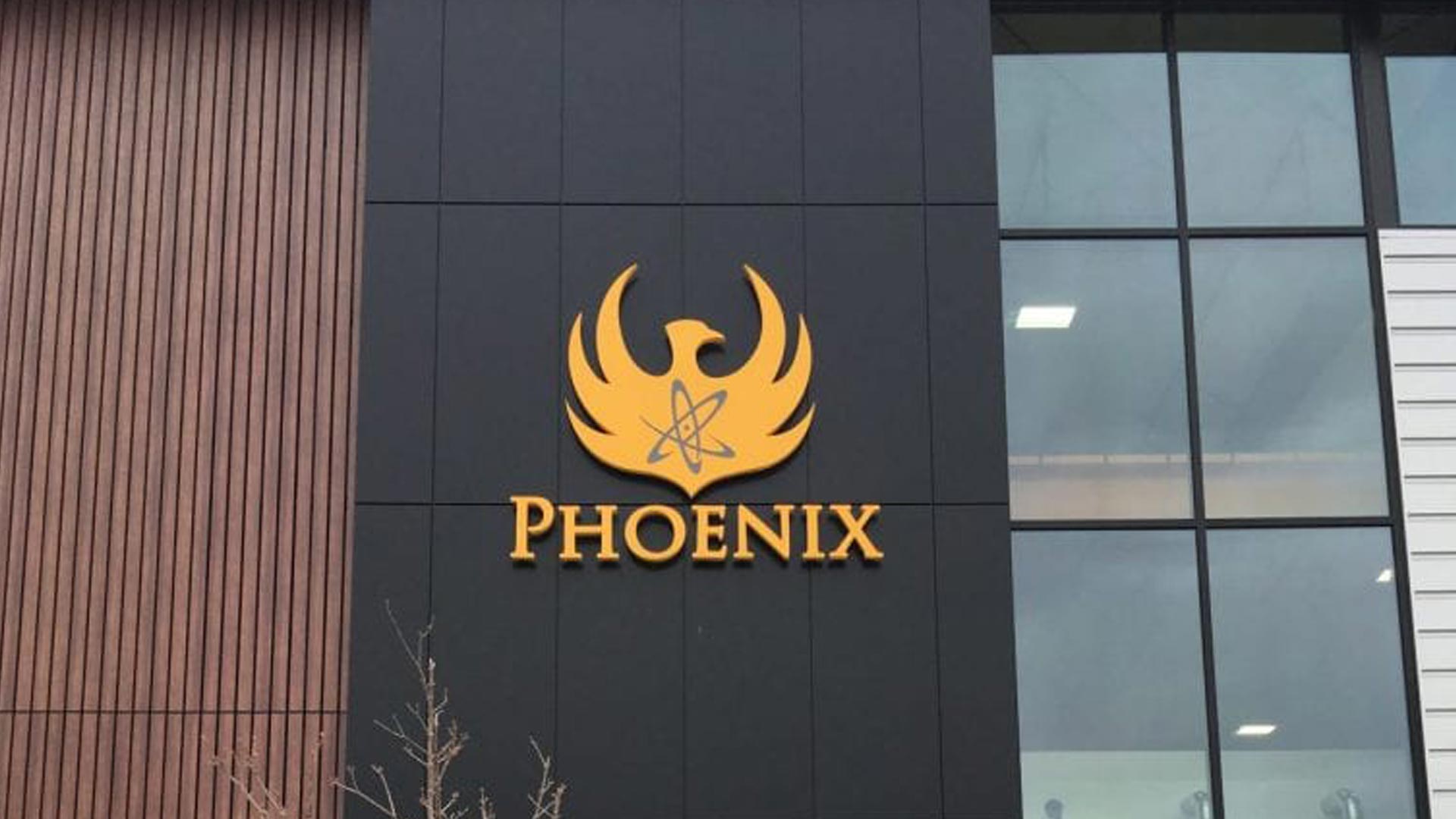
Earlier in Q4 of 2018, our quality management system was audited and certified to meet the International Organization for Standardization’s (ISO) 9001:2015 requirements for a Quality Management System as well as the requirements of the AS9100D (2016) standard, making us currently the only manufacturer of high-flux neutron generators with a quality management system certified to meet AS9100D standards.
An organization’s quality management system outlines the policies, processes, and procedures throughout the company that ensure that clients consistently receive the best products and services possible. To this end, organizations such as the ISO have developed rigorous standards for quality management systems, which apply to over one million organizations in over 160 countries. Over the years of our transition from research and development startup to manufacturing and selling nuclear technology for commercial clients, our QMS was codified with the intention of meeting these critical standards.
ISO 9001:2015 is the most current version of the ISO’s set of QMS standards, which are designed to help organizations of all shapes and sizes organize their processes, improve efficiency, and continually improve their processes. AS9100D is a similar set of standards for quality management systems developed by the Society of Automotive Engineers and European Association of Aerospace Industries. Although its criteria significantly overlap with ISO 9000:2015 standards, AS9100D’s quality standards are tailor-made for aviation, space, and defense organizations to ensure that OEMs in aerospace address the specific requirements of customers such as the Department of Defense, NASA, and commercial aerospace companies. Meeting these standards ensures that we will always be able to support our customers in aerospace who require the highest quality and oversight in the technology and services we provide.
Ensuring that a QMS meets ISO 9001:2015 and AS9100D standards is a long and rigorous process. However, although an audit typically takes a year or longer to solidify and implement, our team was able to bring everything together from the standard practices already being employed to a full-blown, certified QMS in less than six months.
The Stage 1 assessment ensures that the QMS is ready to undergo a more rigorous assessment for certification; the second, or Stage 2, closely examines each part of the QMS and its implementation to make sure it complies with the standards set forth. Once the initial audit finds that the QMS meets ISO and AS standards, the registrar returns to conduct further audits on an annual basis to ensure compliance; internal audits are also conducted throughout the year to further solidify the effectiveness of the QMS.
As our company continues to grow, our QMS’s adherence to ISO 9001:2015 and AS9100D standards will allow us to continue on our mission to transform the world by advancing practical, commercial, near-term applications of nuclear fusion technology, with the ultimate goal of making fusion energy a reality. Everybody here at Phoenix is thrilled to have a rigorous quality management program that allows us to continue to deliver the highest-quality products to our clients for radiography, isotope production, radiation effects testing, IED detection, and more.